Plastic extrusion for extra-durable, resilient materials
Plastic extrusion for extra-durable, resilient materials
Blog Article
Understanding the Basics and Applications of Plastic Extrusion in Modern Production
In the world of contemporary production, the technique of plastic extrusion plays a critical duty. Unraveling the basics of this process discloses the true flexibility and possibility of plastic extrusion.
The Principles of Plastic Extrusion Process
While it may appear complex, the basics of the plastic extrusion procedure are based upon relatively simple principles. It is a manufacturing procedure where plastic is thawed and then formed right into a continual account with a die. The raw plastic material, commonly in the kind of pellets, is fed right into an extruder. Inside the extruder, the plastic goes through warm and stress, causing it to melt. The molten plastic is then required via a designed opening, known as a die, to develop a long, continual item. The extruded item is cooled down and after that cut to the wanted size. The plastic extrusion process is thoroughly made use of in different markets due to its cost-effectiveness, performance, and convenience.
Different Sorts Of Plastic Extrusion Methods
Structure upon the standard understanding of the plastic extrusion process, it is required to discover the different strategies involved in this manufacturing technique. The two primary methods are profile extrusion and sheet extrusion. In profile extrusion, plastic is thawed and created right into a constant profile, usually used to develop pipelines, poles, rails, and home window frameworks. In comparison, sheet extrusion creates big, level sheets of plastic, which are usually more processed into products such as food product packaging, shower drapes, and vehicle parts. Each method calls for specialized equipment and precise control over temperature and pressure to make sure the plastic preserves its form throughout air conditioning. Recognizing these techniques is essential to using plastic extrusion successfully in contemporary production.

The Function of Plastic Extrusion in the Automotive Industry
A frustrating majority of components in contemporary vehicles are products of the plastic extrusion procedure. This process has actually reinvented the vehicle industry, transforming it right into a much more efficient, cost-efficient, and adaptable manufacturing sector. Plastic extrusion is largely made use of in the manufacturing of various car elements such as bumpers, grills, door panels, and dashboard trim. The process provides an attire, regular output, enabling producers to produce high-volume get rid of fantastic precision and minimal waste. The agility of the extruded plastic that site parts adds to the overall reduction in automobile weight, improving gas effectiveness. Furthermore, the durability and resistance of these components to warm, cool, and impact boost the durability of autos. Hence, plastic extrusion plays an essential duty in automobile manufacturing.

Applications of Plastic Extrusion in Durable Goods Manufacturing
Past its considerable impact on the auto market, plastic extrusion proves similarly efficient in the realm of consumer products manufacturing. The versatility of plastic extrusion enables makers to design and generate complicated shapes and sizes with high precision and effectiveness. The adaptability, flexibility, and cost-effectiveness of plastic extrusion make it a preferred selection for numerous customer products makers, contributing significantly to the sector's development and innovation.
Ecological Impact and Sustainability in Plastic Extrusion
The prevalent use of plastic extrusion in manufacturing invites examination of its environmental ramifications. Efficient machinery minimizes power use, while waste monitoring systems recycle click here now scrap plastic, lowering raw material needs. In spite of these improvements, additionally development is required to minimize the ecological impact of plastic extrusion.
Verdict
Finally, plastic extrusion plays a critical duty in modern production, especially in the auto and consumer products industries. Its adaptability allows for the manufacturing of a vast array of parts with high accuracy. Its potential for reusing and development of biodegradable products uses an appealing avenue in the direction of lasting practices, consequently dealing with environmental issues. Understanding the fundamentals of this procedure is vital to optimizing its applications and advantages.
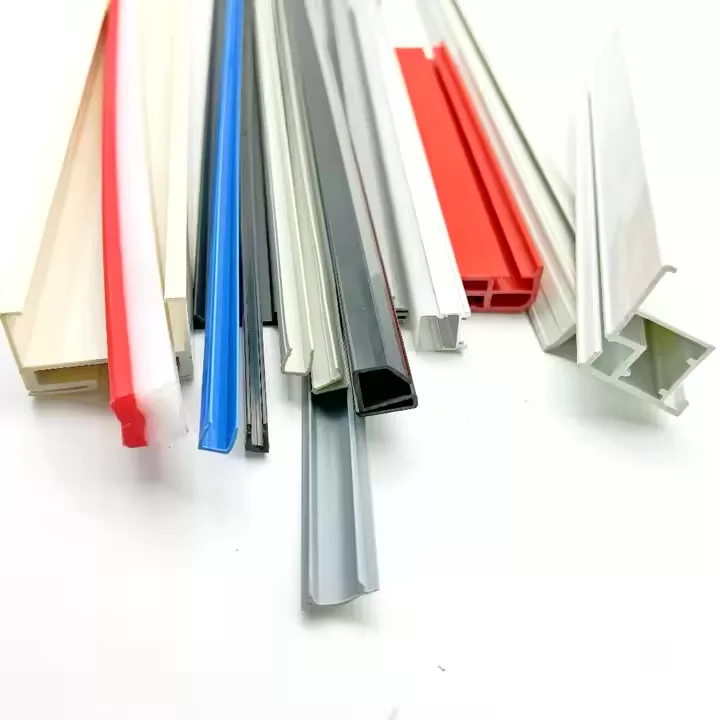
The plastic extrusion process is thoroughly made use of in different industries due to its adaptability, cost-effectiveness, and efficiency.
Structure upon the fundamental understanding of the plastic extrusion process, it is required to explore the numerous methods included in this manufacturing technique. plastic extrusion. In contrast, sheet extrusion produces big, level sheets of plastic, which are usually more refined Extra resources into items such as food packaging, shower drapes, and automobile parts.A frustrating majority of components in modern lorries are products of the plastic extrusion procedure
Report this page